Main Sector of relevance\IRC classification 8. Industrial Manufacturing, Material and Transport Technologies
8.36 High-porous cellular material based on nickel and
aluminium-oxide ceramics
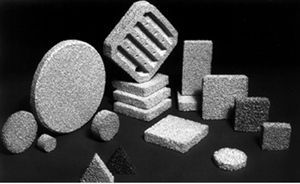
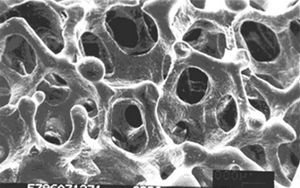
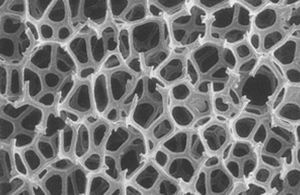
Developers’ contact information
State Scientific Institution “The Powder Metallurgy Institute of the National Academy of Sciences of Belarus”
41 Platonov Street, Minsk BY-220005
O.L. Smorygo
Tel.: +375 (17) 293-98-23
Summary
Open-cellular nonorganic foam materials are made by doubling of
foam-polymeric compound structure and have a complex curly structure consisting
of interdependent cells systems. Open-cellular nonorganic foam materials have
extremum high porosity and permeability, heat resistance, corrosion stability,
catalytic reactivity.
Description
At present foamed metal and cellular ceramic production
technologies have been worked out on the basis of the following materials:
- Metals: Ni, Ni-Al, Ni-Cr,
Ni-Cr-Al, alloys Cu, etc..;
- Ceramics: Al2O3,
Al2O3-SiO2,
ZrO2, cordierite-mullite, mullite-zircon, etc.
- Cellular ceramics and foamed metals with protective and
catalyst active coatings: Ag, glass (glazing), γ-
Al2O3/Pd(Pt), γ-
Al2O3-La2O3,
mixed oxides, etc.
Manufactured foam materials have the following properties.
Properties |
Foamed metal |
Cellular ceramics |
Apparent porosity, % |
92-97 |
75-90 |
Transverse modulus of rupture, MPa |
- |
0.5-2.0 |
Ultimate compressive strength, MPa |
0.8-1.5 |
- |
Operating temperatures, °C |
up to 1100 |
up to 1550 |
Pore size, mm |
0.3-5.0 |
1.0-5.0 |
Coefficient of permeability, m2 |
10-7-10-9 |
10-7-10-9 |
Maximum linear dimensions, mm |
500 x 500* |
150 |
Thickness, mm |
1-25 |
10-25 |
* in case of pure Ni
Technology type
Technical advantages and economic benefits
Advantages over analogues: wide range of materials and wide range
of thermophysical and hydrodynamic parameters.
Technology differentiation and uniqueness
The materials have unique operational characteristics in a wide
range of practical applications.
Context in which technology was identified
9-th, 10-th, 11-th International Specialized Exhibitions “Metal
powder industry - 2003, 2005, 2007”.
Technological keywords
Foamed metal, cellular ceramics, filter, block catalyst.
Development Stage
- Experimental development stage
- Results of demonstration test available
- Currently in use/production
Intellectual property rights
Range of applications
- Filtration of viscous fluid, severe or hot fluids and
gases, vapour recovery of precious metals, etc..
- Catalysis – primarily ecological one.
- Heating gas systems of radioactive type.
- Flame-arresters, e.g., in welding engineering.
- Electrodes – in batteries, trapping ion systems.
- Superlight constructional materials.
Classifier Used at the EU Innovation Relay Centres
- Industrial Manufacturing, Material and Transport Technologies
Preferable Regions
- South America
- Asia
- Africa
- Australia
Practical experience
- Catalyst carriers, ceramic foam
- are used in neutralizing tanks of burning up of effluent
gases, units of deep oxidation of hydrocarbons and other catalyst
systems as block catalyst carriers.
- are made from silicate or cordierite ceramics with finely
divided coating.
- it is possible to apply finely divided coating with
catalyst active elements (including platinum group metals).
- Catalyst carriers, foamed metal
- are used in neutralizing tanks of burning up of effluent
gases, units of deep oxidation of hydrocarbons and other catalyst
systems as block catalyst carriers.
- are made from nickel, cuprum, iron and other metals and
their alloys;
- it is possible to apply finely divided coating with
catalyst active elements (including platinum group metals).
- Ceramic foam filters
- are used as filters for fluids and gas treating, treating
of melts of metals and polymeric compounds, flame-arresters, noise
limiters, insulation kits.
- are made from aluminosilicate ceramics.
- Foam metal filters
- are used as filters for fluids and gas treating,
polymeric compounds, noise limiters, flame-arresters
- are made from nickel, cuprum, iron and other metals and
their alloys.
- Test model of low temperature catalytic combustion
unit.
Scope of application: deacidification of dangerous volatile organic compounds
that are released into the atmosphere by enterprises of various branches of
industry (in particular, emissions of ethanol and ethyl acetate mixture are
typical of printing industries). Conversion rates: more than 99% at space
velocities of gas flow (0.8-2)·104 1/hour for vapour concentration
of organic vapours of organic compounds 0.5-5 g/m3. Operating
temperature: 230 – 270 °C.
Environmental impact
None.
Type of collaboration sought
- R&D contract
- Joint venture
- Other:
Production sale;
Technology sale.
Terms and restrictions
None.
Available technical assistance